The researchers developed a fast and efficient method for producing nanoparticles from aluminum-based metallic glasses. The team of researchers lead by Professor Dmitry Luzgin published their paper in the Intermetallics journal.
Amorphous metals are often called futuristic materials. Due to their lack of a crystalline structure, these materials exhibit various unusual properties, which have already found applications in transformer cores, various sensors and ultrahard composites. Despite being very hard, most metallic glass isactually incredibly brittle, which is why the global scientific community is now focused on producing composite materials using thermal crystallization. The scientists' main goal is to obtain a pliable material. Their lack of success has everyone wondering how this crystallization occurs: what kinds of phases are formed as a result of crystallization, and what are their properties?
READ MORE: Russian Scientists Create Environmentally Friendly Film Packaging
"We are trying to achieve this goal, too," said Andrei Bazlov, researcher at NUST MISIS' Department of Material Science of Non-Ferrous Metals. "We were the first in the world to discover an interesting property of aluminum-based metallic glassy alloy: the rapid heating of this metallic glass produces one kind of material, while slow heating produces a different kind. It is highly unusual, since, as a rule, changing the speed of heating does not result in different products."
The main feature of the new material is that during the process of rapid crystallization, it forms spherical aluminum nanoparticles about 10 nanometers in size. This material is two times harder than the product of slow heating, Bazlov said. At the same time, the two materials are equally brittle.
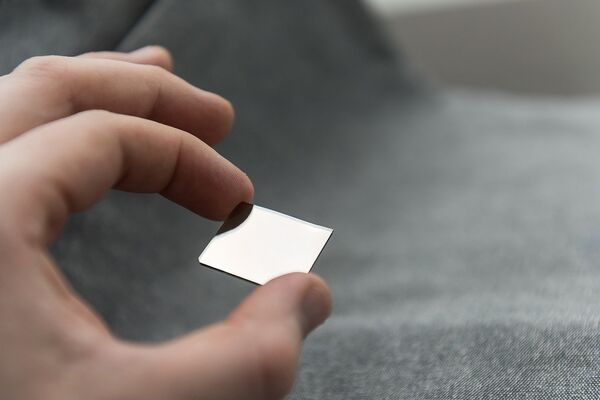
First and foremost, this research promises to make the production of nanoparticles simpler and cheaper. In the past, nanoaluminum was produced using complicated methods: either by chemical vapor deposition or explosive dispersion. These are both very energy-intensive processes. Researchers at NUST MISIS discovered a way to produce this material using classical metallurgical methods, which require significantly less energy. "It is, in fact, casting," Andrei Bazlov said. "Not in its traditional form, but still casting. Plus simple thermal processing — annealing."
The practical applications of the innovation are quite clear. Nanoaluminum is characterized by several important features. Unlike other materials with microscale particles that ignite at 1000 degrees Celsius, it takes nanoaluminum only 660 degrees Celsius to start a reaction with the release of heat. Since the burning rate of nanoaluminum is almost one third higher, it can be added to rocket fuel to increase the rocket impulse by 70 percent.
It is highly important that the particles used as a basis for composites are completely identical in size, because this results in better control of the obtained material's properties. Moreover, like any other nanomaterial, nanoaluminum can successfully be used as a catalyst.
This method can be used for processing other aluminum-based metallic glassy alloys as well, thus obtaining a whole new range of aluminum-based metallic glassy composites.