A newly-established Russian company, Zdravprint, or Healthprint, has come up with its own ideas on how to replace an individual lightweight cast.
The venture fund Maxfield Capital, a firm that invests in global seed and early stage technology companies, has already allocated $100,000 in investments for the development of water friendly 3D- printed cast alternatives, which heal a lot faster and help to avoid the annoying itchiness while healing the fractured bones.
3D Printed Cast, developed by Zdravprint, a brainchild of the Russians Fyodor Aptekarev and Aleksandr Charkassov, has even more advantages compared to conventional fracture plasters.
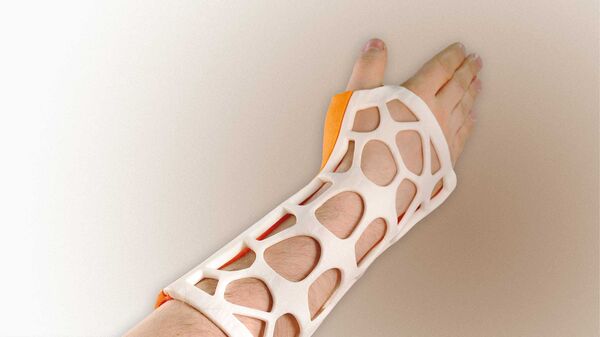
It allows air to be supplied to the injured parts of the body, hence the skin under the plaster does not become dry and scaly.
It causes a lot less, if any, macerations, ulcerations, infections, rashes, itching, burns, and allergic contact dermatitis.
It is a lot lighter and does not restrict movement as much.
The process is as following: First a patient has the injured limb scanned in three dimensions. Then, a computer makes a model of the splint or cast using special plastic in a 3D printer. The plastic cast can be made in any color, and once printed all that needs to be done is for it to be heated and smoothed into shape.
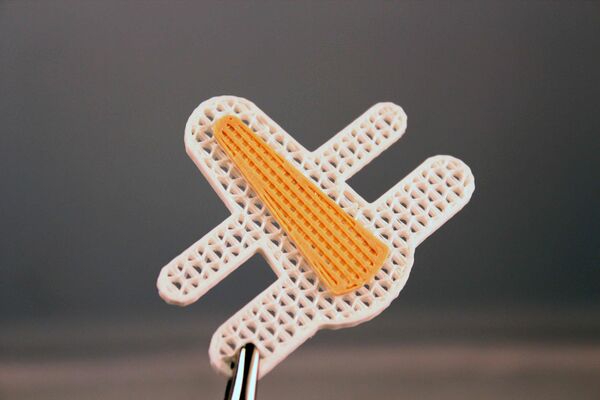
A plaster cast, however, is still needed in the first stages of repairing a break, as it enables doctors to control and adjust the initial bone union. This lasts for about a week until the swelling subsides. It is only after this that the 3D-printed version can take its turn.
Production of the new type of cast takes about 12 hours in terms of the actual printing, and the subsequent fitting can be completed in less than an hour.
Aptekarev claims he got the inspiration for the idea from a 3D printed dress designed by Francis Bitonti.
Shoegazing into the Future of 3D Printed Fashion @Fashiontribes http://t.co/fzcFoQr8I3 pic.twitter.com/qzLR0oPfSe
— Francis Bitonti (@francisbitonti) 27 сентября 2014
As a skateboarder, he has suffered a number of broken bones, and suffered from an uncomfortable heavy plaster cast, which invariably itched. Thus he came up with the idea of introducing a custom-made cast using a 3D printer to help people overcome their medical problems.
Aptekarev predicts that within seven years, his 3D printed casts will have taken over from plaster completely.
Francis Bitonti, the dress designer applying architecture to 3D printed couture @guardian http://t.co/R6ikTeInHO pic.twitter.com/x8qkuWLAXP
— Francis Bitonti (@francisbitonti) 26 сентября 2014