Oleg Papin, chief mineral surveyor of the Combine, has explained what it means to deal with a blue clay (or blue earth), water cannons and hoop nets.
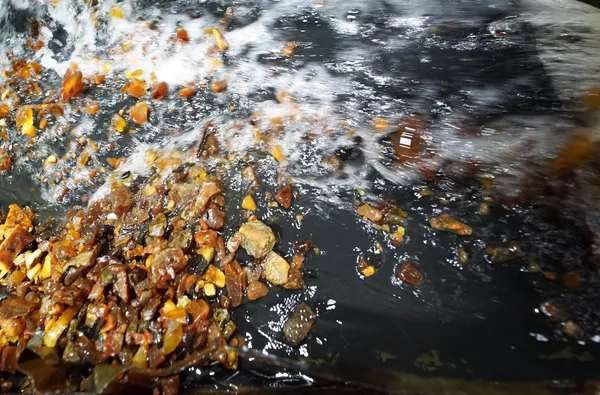
The most productive stratum, which has rich deposits of amber, is blue clay, also referred to as "blue earth". It has received its name due to the considerable content of glauconite mineral, which imparts the bluish grey tint to it. The stratum of blue earth with the thickness from 2 to 12 meters, lays at a depth of 50 – 70 meters from the surface.
Nowadays the amber extraction is carried on in an open-cast mine, being a composite, highly-mechanized production. Originally the over-burden layers were exploited using an excavator, and were transported in the slag-heap by rails.
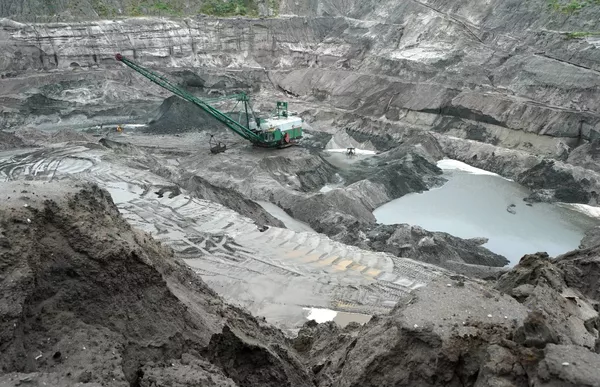
The principle of hydro-mechanization was introduced into practice after two huge landslides in 1957 and 1958, when the bottom of the mine was buried by almost half a million tons of earth, and the equipment and the whole transport system were out of order.
To get to the amber stratum it’s necessary to remove the upper layers of barren rock. Oleg Papin explained that hydro-monitors wash them away with their streams of water, and the liquid pulp (the mixture of rock and water), which was formed, is thrown down to the sea by the pipeline.
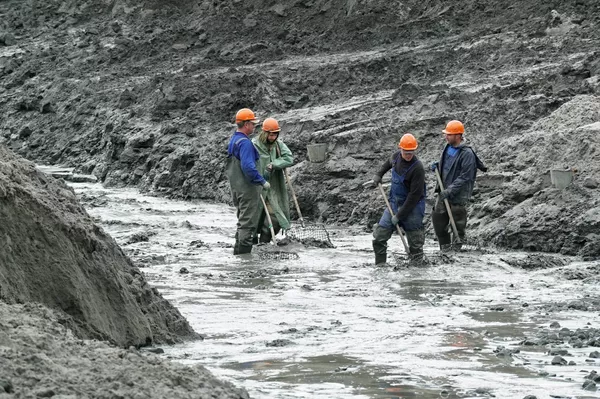
Before 1995 the blue earth, containing amber, had been extracted by the chain-bucket excavator, and then transported to the concentrating mill using a belt conveyer. Nowadays, in order to preserve the amber in a good state, the method of hydro-mechanization has been used; and the amber has been transported by pipeline.
The blue earth, which was washed away by the water, is going to the Combine through the grate with meshes 5 cm in diameter; where the workers are picking out the biggest pieces of the mineral.
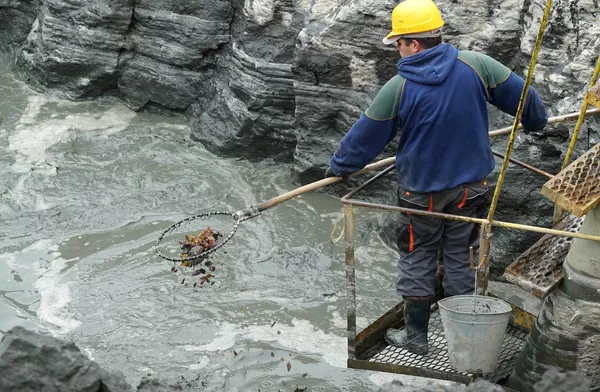
Then the most part of the barren rock, having gone through the sieve with the 2mm meshes, is going to the waste.
The material, which has remained, is passed through the system of arc sieves, where it goes through its initial washing and dehydrating.
Then in the separator this mass is exfoliated in a special solution of a density lower than amber; the heavy fractions are accumulating at the bottom, and the small amber emerges at the surface with pieces of wood are emerging.
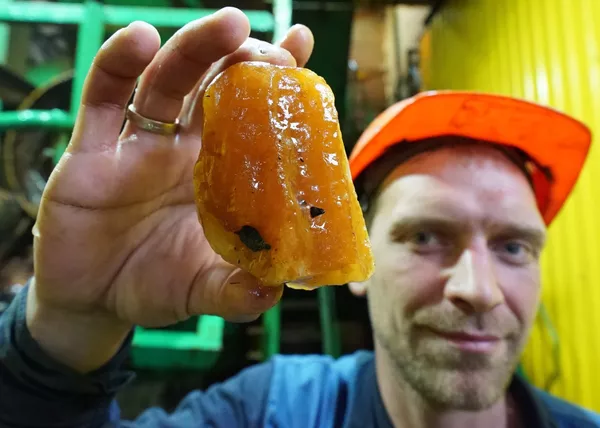
The amber, separated from admixtures, is delivered to the sifter – the system of sieves moving in opposite directions, with the meshes of different diameters, which are located one above the other. By means of vibration the amber is sifted and divided into three fractions, depending on the size.
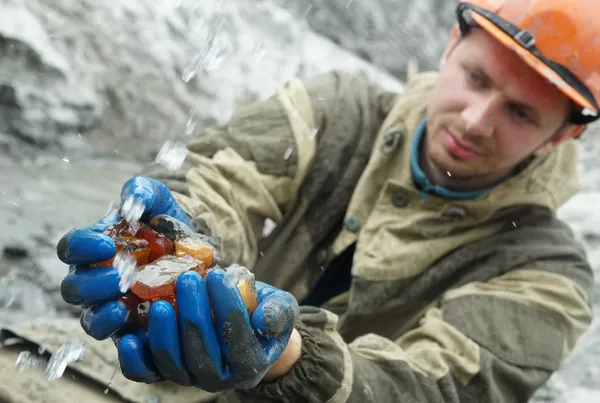
All extracted raw amber falls into the following categories: amber for jewelry production and amber for industrial purposes.
Industrial amber is usually of fine fraction, black and of no interest to goldsmiths. It is used for producing high quality varnish and as well as musical instruments and car varnish of premium class.