A new type of flux (a purifying agent used in metallurgy) developed by the researchers allows for the creation of a unique alloy with improved stress-strain characteristics and corrosion resistance properties.
The flux developed by the materials scientists uses carnallite, an evaporate mineral readily available in the Russian Ural Mountains, which when combined with a 30% mixture of calcium chloride creates a flux with a strong purifying effect. The improved flux allows for the casting of magnesium alloys with improved corrosion resistance, reduces material losses in alloying components, and allows for the creation of an alloy with a more stable chemical composition.
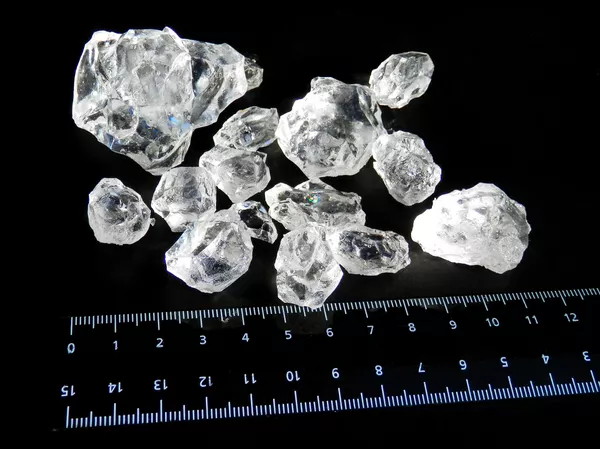
"The use of the technology developed by the NUS&T MISiS in partnership with our industrial partner OK Stroibis [Russia's largest producer of auxiliary materials for non-ferrous metallurgy] will help eliminate the formation of toxic barium-containing slag, improve the quality of the magnesium alloy produced, increase its competitiveness in domestic and export markets, and, ultimately, improve the prospects for import substitution in the aerospace and automotive sectors of Russian industry," he said.
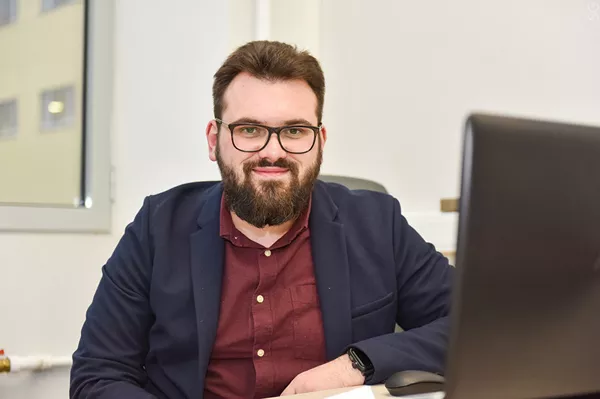
Magnesium, a very lightweight metal, has a density significantly below that of titanium and aluminum (1.73 grams per cubic cm compared with 4.5 and 2.7 grams, respectively). Traditionally, the poor corrosion resistance characteristics of Russian-made magnesium alloys have precluded them from widespread use in aviation, rocketry and the automotive industry. NUS&T MISiS researchers have set on correcting that shortcoming.
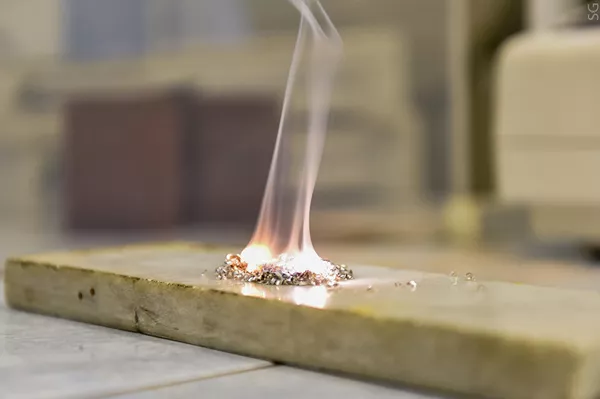
The NUS&T MISiS scientists' next step is to create a trial production facility to create a trial batch of quality fluxes for large-scale lab tests.