Composite materials are materials made of many components. Individual components usually include a plastic reinforced ultra-strong base. Combining different substances results in a new material whose properties are different from those of the individual components. Many composites have better mechanical properties and weigh less than traditional materials and alloys.
Hexagonal boron nitride nanoparticles are one of the possible strengthening modifiers. Material experts have long been aware of its unique properties. They can be used for various tasks, such as targeted drug delivery. However, it takes a lot of effort and money to produce BN nanoparticles.
By processing nanoparticles with high energy consumption in various media, researchers have managed to decrease the particles' size more than a hundred times and produce 5-10 nm thick BN nanosheets.
"The results prove ball milling hexagonal BN nanosheets to be highly effective; this method makes it possible to produce many nanoparticles with an average thickness of 50-100 nm", one of the scientists, senior research fellow at the Inorganic Nanomaterials Laboratory Andrei Kovalsky, told Sputnik.
READ MORE: Russian, Czech Scientists Make Biodegradable Nanofiber Bandage for Fast Healing
The scientists used the nanoparticles they obtained to synthesize the first composite metallic-ceramic aluminium-based materials that showed significant strengthening. According to the estimations of NUST MISiS, the cost of manufacturing these nanostructures could be 20 times lower with the use of this new technology, compared with the traditional methods of high-temperature synthesis.
Hexagonal boron nitride is a typical layered material structurally similar to graphene. Hexagonal BN nanoparticles look like "packages" of sheets.
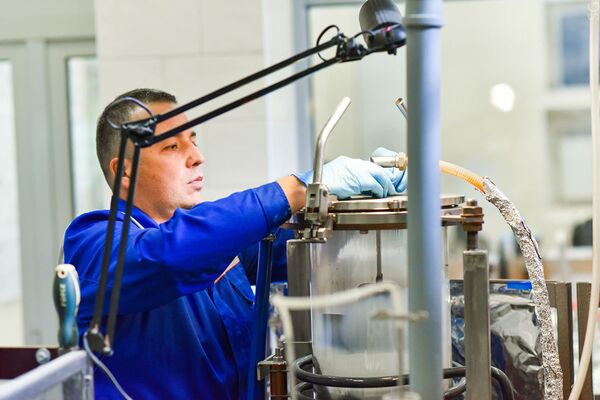
In order to produce nanoparticles, these "packages" must be separated and grinded. If mechanic or ultrasonic grinding is used, the final product always contains pieces of the materials of which the tool was made. Due to a combination of environment conditions (argon, isopropanol, and ethylene glycol) and the improvement of processing parameters, researches have managed to significantly lower the presence of foreign matter by using this technology. This new method is also inexpensive, which allows for it to be used in manufacturing in the near future.